Our extensive experience and wealth of knowledge enables us to offer custom rubber compounds from formulation to application, whatever the industry.
From a modification to an existing rubber compound to suit your process needs, or if you are interested in starting a new project, and creating custom rubber compounds from scratch, our experienced technical team and their service capabilities are equipped to handle any request.
We offer the full range of heat-curable elastomers, from natural rubber (NR) through to perfluoroelastomers (FFKM) and will always advise on the most cost-effective choice for your application. Whether your requirement is for 10kg or +10,000kg, you can be confident that the custom rubber compounds we supply will meet your exact requirements. We also have a range of small-scale equipment available, for specialist compounds and development work.
Our reputation for technical support and advice is second to none within the industry. Our technical team work closely with major industry suppliers to ensure we have access to an extensive range of raw materials and are involved in several collaborative research projects. They regularly attend conferences and technical seminars and have written and presented a number of technical papers.
If you are responsible for specifying compounds where material performance is critical – contact us.

Full Rubber Compounding Service
We offer a full rubber compounding service, from formulation to application. Our customers usually approach us from one of the following start points:
You have a specification:
This gives us physical and/or chemical properties for the product.
Clwyd Compounders have mixes approved to meet many standard specification and our working database contains over 5000 formulations. Our trained staff and well-equipped laboratory enable us to carry out full testing to almost all industry standards in house.
You have an existing formulation:
We can produce it, and recommend substitutions for any ingredients which are unavailable/ in shortage, or have been classified SVHC under REACH legislation. We never substitute a requested ingredient without informing the customer.
“Hard to handle” formulations are a speciality; our experienced process control team will do what is necessary to obtain a satisfactory product.
You have to match or improve upon an existing part:
You have a sample and some information about its service use. We are experienced in compound identification; we have the analytical equipment (including TGA and FTIR) to identify the sample, and the skills to produce an equivalent.
You have an idea:
For new or improved products which would require enhanced performance from your existing rubber compounds.
We offer a full compound development service, and are well placed to advise on materials selection; we work closely with suppliers, and regularly evaluate new grades and additives where we believe these could add value.
Rubber compounds for a variety of industries
We supply widely-used polymers for use in a wide range of industries:

Your Industry
As the ‘bespoke compounder’, we are built for any customer request with the facilities and technical knowledge to formulate and supply into your industry. Working with us, you will gain an in-depth knowledge into your custom rubber compounds, to ensure the material performance meets the requirements of your industry.
As a specialist rubber compounder, we deal with a variety of industries including: automotive, space, furniture, audio equipment, architecture, public transportation and the list goes on. In short, rubber is utilised in thousands of everyday items that most people take for granted on a daily basis. If you want to find out how we can enhance your products with custom rubber compounds – contact us.
Typically it is only when things go wrong that people look to understand rubber in-depth for their application: such as the Challenger Space Shuttle disaster, Oil spills or even the loss of a Formula 1 race. However, we are here to offer technical support to anyone who wants to know how to leverage the benefits of quality custom rubber compounds to enhance their product. Other polymers which are widely used in this industry include NBR, EPDM, VMQ (Silicone) and FKM.

Aerospace
The key requirement is compounds which meet the stringent and demanding specifications that are in place. The need to provide complete certification, backed by comprehensive traceability systems is fundamental.
Fluorosilicone compounds are widely used in this sector, due to their ability to perform over a wide range of temperatures (typically -55°C to 200°C) and their excellent fuel and oil resistance. We have extensive experience of formulating fluorosilicones; compounds are available with hardnesses from 20 to 85 Shore A, and include a number which have been specifically formulated to be able to meet aviation and military specifications such as AMS/MIL, ABR and DTD.
Other polymers which are widely used in this industry include NBR, EPDM, VMQ (Silicone) and FKM.

Specialist Automotive
Technology in the Specialist Automotive industry is fast evolving – the latest Formula 1 innovations will appear in production models just a few years later. We aim to be at the forefront by supplying compounds used by a number of teams. We have proven experience in this field and an extensive portfolio of high performance elastomers which offer the ultimate in petro-chemical and high temperature resistance to meet the demands of this market.
In Formula 1, cost is not the dominant concern. Where cost is key, we can provide compounds suitable for co-extrusion and co-moulding where a cheaper polymer compound is used to support a high performance polymer compound which provides the operating surface. We maintain a close working relationship with our suppliers, sourcing and developing the latest polymers to provide the best possible chemical and physical properties suitable for components in this industry.
NBR, HNBR, FKM and VMQ (silicon) are widely used in this industry.
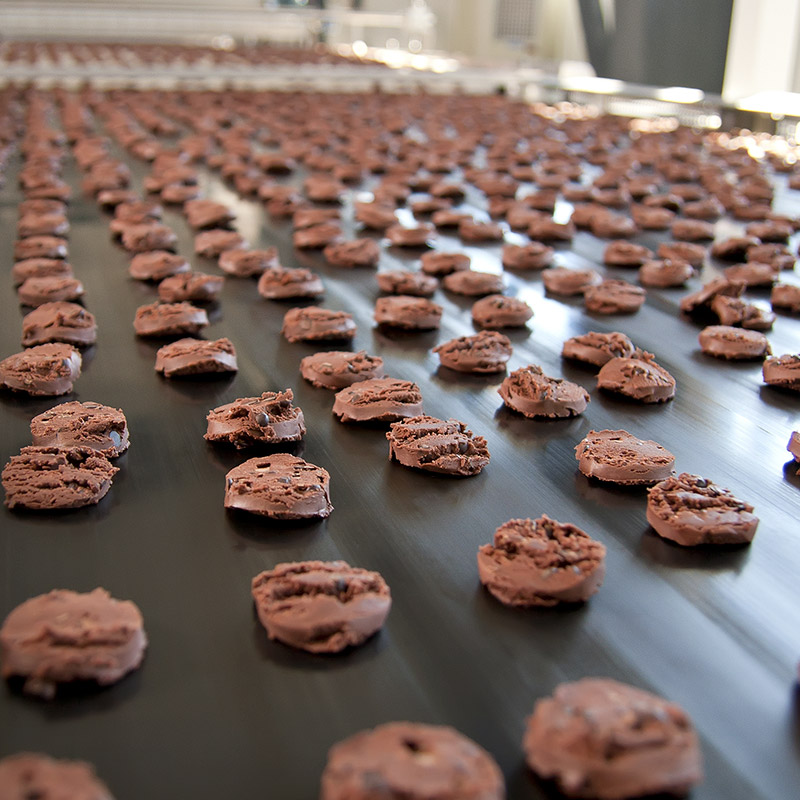
Food & Water
We supply a wide range of compounds which comply to the most recognised standards in this industry; the American FDA (Food and Drug Administration) standard and EC 1935/2004 Legislation, which govern materials that can be used in contact with food. WRaS (Water Regulations and Advisory Scheme) approved compounds, for applications in contact with potable water, are also available.
Traceability of contaminants is a key issue in this industry; all compounds can be supplied in “food blue” or other colours as required to provide easy visibility. Compounds can also be supplied which contain ferrite fillers; incorporating these into the compound means that fragments of rubber produced by, for example, abrasion or break down of seals will be detected by the standard metal detection software in use on food production lines.
Compounds widely used in the food industry include EPDM, NBR and FKM.

The table below lists several compounds we have formulated to be resistant to rapid gas decompression:
Compound Description | Temperature Range(°C) | General comments |
-20 to 150 | Good workhorse. Optimum mechanicals across operating temperature range | |
-20 to 150 | Good workhorse. Optimum mechanicals across operating temperature range | |
-35 to 150 | Improved low temperature; inferior resistance to oil etc | |
-15 to 200 | Good mech, high temp, improved chemical resistance | |
-2 to 220 | Good mech, high temp, high fluorine for optimum chemical resistance, ok steam | |
FKM Type 2 90 (ED) (3) | -3 to 220 | Good mech, high temp, high fluorine for optimum chemical resistance, ok steam |
FKM Type 2 90 (ED) (4) | -3 to 220 | Good mech, high temp perf, high fluorine for optimum chemical resistance, ok steam |
-12 to 240 | Good mech, high temp performance, oils | |
-14 to 240 | Good mech, high temp performance, oils | |
-30 to 220 | Improved low temperature | |
FKM Type 3 95 LT (ED) | -30 to 220 | Improved low temperature |
-40 to 220 | Best in class low temperature | |
0 to 250 | Good mech, high temp, amines, H2S, steam | |
FEPM (Aflas®) 95 (ED) | 0 to 250 | Good mech, high temp, amines, H2S, steam |
-7 to 220 | Good mech, high temp, amines, H2S, steam | |
-7 to 220 | Good mech, high temp, amines, H2S, steam | |
-2 to 250 | Very broad chemical resistance (including amines, H2S, steam) high temp | |
-30 to 250 | As above, extended temperature range |
*General temperature range for the elastomer under normal service conditions estimated using the TR-10 value of the base polymer. Any high pressures likely to be encountered in service should be considered.
These compounds are suitable candidates for testing to RGD and/or sour gas standards. The correct material selection is dependent on factors such as required test standard, chemical resistance and low temperature requirements. Please contact us for more information.
Oil & Gas
Rubber compounds used in this sector are required to exhibit good heat and chemical resistance, together with excellent physical properties. The most widely used polymer is NBR, however, with increased well temperatures and ever increasingly aggressive chemical environments, higher performance elastomers are being used such as HNBR, FEPM C (copolymer), FEPM T (terpolymer) and FKM.
In this industry there is a frequent requirement for hard, thick section mouldings such as packer seals, which are traditionally difficult to mould. We have specially developed compounds for these applications, which enable the production of fully consolidated fissure-free parts. This is particularly important in environments where there is a risk of explosive decompression. For more information see our technical paper and case study.
We have recently developed a new series of ED compounds, which include both bisphenol and peroxide-cured FKMs, FEPM (Aflas®), HNBR and FFKM. These compounds have been formulated to give excellent basic physical properties, along with processing ability, and have also been tested to ISO 23936-2 for rapid gas decompression (RGD). This range of developed compounds would therefore be ideal candidates to take forward to gain NORSOK approvals.

Nuclear / Power Generation
In this safety critical market, close attention to raw materials and cleanliness is essential. Compounds must be strictly controlled to specification. Even minor changes to raw materials which are not picked up by standard physical tests, can result in reduced performance of components in service.
We work closely with raw material suppliers to ensure minimal variation in incoming polymer properties, and will not change approved formulations without testing, evaluation and customer authorisation. In addition to our standard quality control checks, specific testing regimes can be established for these critical compounds, including dispersion checks. Our databases provide full batch traceability, and include weighing and mixing records. Customer audits and site visits are always welcomed.
Compound selection will be governed by the expected radiation level in the working environment. Some polymers are prone to continued curing in the presence of radiation, which will result in loss of elasticity and therefore sealing properties.
EPDM, NBR and FKM polymers are widely used in this industry

Defence
Tough, durable and resilient materials which maintain high levels of chemical and thermal resistance in harsh environments are vital to this industry.
We have been involved in developing compounds for a number of projects, ranging from tank tracks to personal protection equipment, and continue to work closely with both raw material suppliers and with our customers to ensure that we are offering the latest technology.
Many applications demand compounds which must conform to stringent specifications – in some instances these were laid down many years ago. We can advise on how these can be updated; for example, where the specified test fluids are no longer available.
Polymers which are widely used in this industry include NR, NBR, CR, VMQ (silicone) and FKM.